2002年至2004年特种设备严重以上事故统计对比表
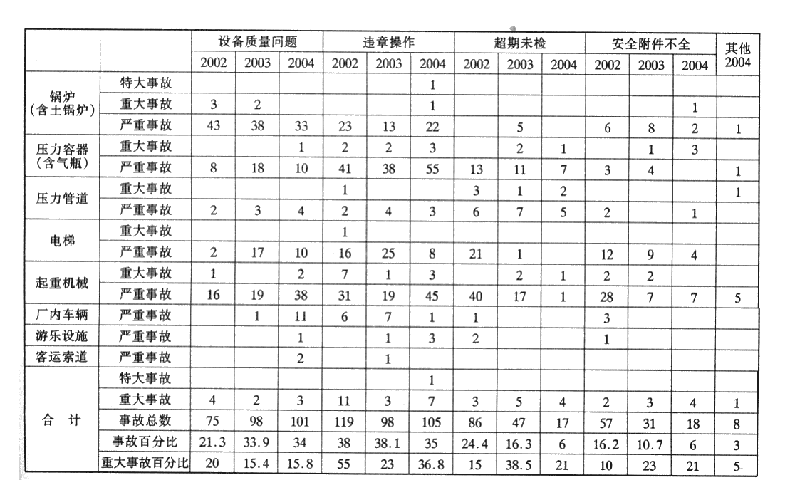
从上述特种设备事故统计分析可以看出:
(1)特种设备事故原因主要是:违章操作、设备质量问题、超期未检、安全附件失效等;而重大事故原因依次是:违章操作、超期未检、安全附件失效、设备质量问题。
(2)重特大事故主要集中在起重机械、锅炉、压力容器、压力管道。
(3)锅炉:因设备质量问题引发的事故逐年下降,表明“土锅炉”专项整治成效显著;因违章操作引发的事故上升:
(4)压力容器:违章操作和气瓶充装管理混乱是引发压力容器事故的主要原因,安全附件或安全装置损坏失效引发的重大事件逐年上升;
(5)压力管道:因超期未检,致使存在缺陷未及时发现是引发压力容器管道事故的关键因素;
(6)起重机械:因违章操作和设备质量问题引发的事故起数明显上升;
(7)电梯:事故起数明显减少;
(8)厂内机动车辆、游乐设施和客运索道事故较少。
4 特种设备重大危险源的风险控制、管理与事故应急
风险控制主要是通过探讨失效发生的原因,从而采取相应措施,降低失效的概率,减少事故损失。风险管理是控制风险、减少损失所采用的各类检验、监控方法与过程的统称。风险管理,一般从降低失效的概率和减少事故损失两个方面考虑。
降低失效的概率,在设计阶段,尽可能规避高风险的工艺生产系统与装置;在生产运行阶段,根据对潜在危险的预测,要及时采取检验、维修与控制,或者改变工艺条件,规避失效的发生。
根据管理学关于控制关键的少数和控制变化趋势的理论,当前特种设备安全监控的重点是:
(1)对重大危险源实行重点监控,逐台登记建档,定期现场巡查,动态掌握安全状况。
(2)规范特种设备操作、管理人员(尤其是锅炉操作、气瓶充装、起重机械操作人员)的培训考核,提高作业人员的素质。严格管理,杜绝无证操作、违章操作,防止人为事故的发生。
(3)加强特种设备生产质量的监督(尤其是起重机械的安装质量的监督检验),继续打击非法生产特种设备的行为。
(4)强力推动压力管道的检验工作,加强压力容器、起重机械安全附件的检查。
减少事故损失以降低损失幅度为主。紧急隔离,紧急减压。带压堵漏,设置截断阀、消防设施等都是常用的方法。应急计划是重大危险源控制的一个重要组成部分。应急计划的目的是抑制突发事件,尽量减少事故的危害。一个完整的应急计划由两部分组成:现场应急计划(由企业负责制定)和场外应急计划(由政府主管部门制定)。应急计划应提出详尽、实用、明确和有效的技术和组织措施。企业应对每一个重大危险源制定出一套安全管理制度,进行严格的管理控制,包括:安全操作制度、安全维护和监控制度、安全检查制度和员工的安全培训制度等。企业应定期检验和评估现场应急计划和程序的有效程度,并在必要时进行修订。政府主管部门应定期对辖区内重大危险源进行监察、调查,评估企业执行重大危险源管理制度的情况,确保重大危险源控制措施得以落实。并根据辖区内重大危险源情况,建立重大事故应急系统。以便对突发事件进行救援处理,控制事故的严重度及事故对公众和环境的影响。场外应急计划应包括:应急机构的组织、通讯系统的建立、专项设备的信息、专家信息源、应急救援专业队伍、事故预防、预测、预警、应急响应、后期处置、保障措施等。
特种设备应急处理一般包括紧急疏散、现场急救、险情排除、火灾扑救等。
(1)紧急疏散。发生危害介质泄漏时,应立即组织警戒区及污染区与事故应急处理无关的人员撤离。对发生易燃易爆和液态氧介质压力容器、压力管道爆炸或泄漏的,应组织群众向上风向,迎风转移;对发生有毒介质压力容器、压力管道爆炸或泄漏的,应组织群众佩戴个体防护用品或用湿毛巾捂住鼻嘴向上风向,迎风转移。
(2)现场急救。针对事故伤害特征,组织医疗机构实施救治。
(3)险情排除。根据发生事故的特种设备的技术、结构和工艺特点以及发生事故的类别,制定抢险救援技术方案,采取措施,防止事故扩大。对发生易燃易爆和有毒介质压力容器、压力管道泄漏的,应立即采取措施处置泄漏。处置泄漏包括泄漏源控制及泄漏物处理。修补和堵塞泄漏口,制止介质进一步泄漏,对整个应急处理是非常关键的。能否成功地进行堵漏取决于几个因数:接近泄漏点的危险程度、泄漏孔的尺寸、泄漏点处实际的或潜在的压力、泄漏物质的特征。
(4)火灾扑救。针对介质特性,选择正确的灭火对策。对液化气体类火灾,切忌盲目扑灭火势,在没有采取堵漏措施的情况下,必须保持稳定燃烧。否则。大量可燃气体泄漏出来与空气混合,遇着火源就会发生爆炸.后果不堪设想。
特种设备事故的特点是发生突然,一旦发生事故,往往会引起人们的慌乱,若处理不当,甚至会引起二次灾害。因此,对应急计划要加强培训教育,并定期进行演习,保证能够在紧急情况下,有条不紊地采取措施,将事故损失减少到最低程度。